掌握精益生产管理:从起源到成功实践的全面指南
掌握精益生产管理:从起源到成功实践的全面指南
引言
在当今竞争激烈的商业环境中,企业需要不断提高效率和降低成本以保持竞争力。精益生产管理作为一种先进的生产管理模式,已成为众多企业的首选。本文旨在深入探讨精益生产管理的定义、核心原则、工具与技术,并通过详细的步骤指导如何有效实施精益生产。此外,我们还将分享一些成功和失败的案例,帮助读者更好地理解和应用这一管理理念。
精益生产的起源与发展
精益生产管理的理念最早可以追溯到泰勒制和福特制。这两种生产模式极大地提高了生产效率,但也带来了一些问题,如过度依赖大规模生产和刚性生产线。随着市场需求的变化和技术的进步,丰田公司于20世纪中期提出了丰田生产系统(TPS),成为精益生产的雏形。TPS通过不断改进流程和消除浪费,实现了高效、灵活的生产方式。
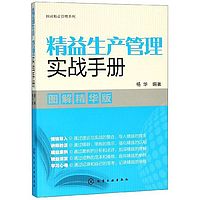
精益生产的核心原则
精益生产的核心原则包括:
- 消除浪费:识别并减少生产过程中的各种浪费,提高资源利用率。
- 实现流动:确保产品在生产过程中顺畅无阻地流动,减少库存积压。
- 创建拉动系统:通过需求拉动生产,避免过量生产造成的浪费。
- 追求完美:持续改进,不断提升生产效率和产品质量。
精益工具与技术
为了有效实施精益生产,企业需要掌握一些关键工具和技术:
- 价值流图:通过绘制当前状态图和未来状态图,帮助企业识别和改善生产流程。
- 5S管理:整理、整顿、清扫、清洁、素养,创造整洁有序的工作环境。
- 快速换模(SMED):通过缩短设备调整时间,提高生产灵活性。
- 标准作业程序:制定标准化的操作流程,确保操作的一致性和稳定性。
- 可视化管理:通过图表、标志等方式,直观展示生产状态和问题,便于管理和改进。
实施精益生产的步骤
实施精益生产需要经过以下几个步骤:
- 识别问题与需求:明确企业存在的问题和改进的需求。
- 制定实施计划:制定详细的实施计划,包括目标设定、资源分配等。
- 培训与文化建设:对员工进行培训,培养精益文化的氛围。
- 改进与持续优化:不断改进流程,持续优化生产效率。
精益生产案例分析
本部分将通过具体案例,分享成功和失败的经验:
- 成功案例:丰田、通用电气等公司的精益生产实践,展示了精益生产带来的显著效果。
- 失败案例:分析一些企业在实施精益生产过程中遇到的问题和教训,从中汲取经验。
精益生产面临的挑战与对策
企业在实施精益生产过程中可能会面临以下挑战:
- 组织文化冲突:传统的企业文化和新的管理理念可能存在冲突。
- 技术与设备更新:需要投入大量资金进行技术和设备的升级。
- 人才短缺与培训:缺乏具备精益生产技能的人才,需要加强培训和招聘。
结语
精益生产作为现代企业管理的重要组成部分,将在未来继续发挥重要作用。它不仅能够提升企业的生产效率和产品质量,还能为企业和个人带来长远的积极影响。希望读者能通过本文的学习,将精益生产的理念和方法付诸实践,推动企业实现可持续发展。
通过以上内容,我们希望能为读者提供一个全面了解和掌握精益生产管理的指南。无论是企业管理者还是普通员工,都可以从中受益,共同推动企业迈向更高的效率和质量水平。
喜欢"掌握精益生产管理:从起源到成功实践的全面指南"的人也看了
-
崇贤馆藏书 警世通言(宣纸排印) 电子书 下载 txt pdf mobi
-
美国高考核心阅读(套装全2册) pdf epub mobi txt azw3 2024 电子版 下载
-
科学搭配食物,打造健康饮食生活——文仁暎的健康饮食指南
-
寻宝小子 电子书 下载 txt pdf mobi
-
玫瑰的故事 pdf epub mobi txt azw3 2024 电子版 下载
-
全方位成长指南:《天天爱学习》系列丛书助你成为全面发展的小学霸
-
生物医学工程伦理 电子书 下载 txt pdf mobi
-
埃托·索特萨斯及其事务所 pdf epub mobi txt azw3 2024 电子版 下载
-
植物大战僵尸2博物馆漫画:大英博物馆奇妙探险
-
政府管制评论 2018年第2辑(总第15辑) 经济科学出版社 电子书 下载 txt pdf mobi
- 变态心理学 pdf epub mobi txt azw3 2024 电子版 下载
- 全真模拟预测试卷 电子书 下载 txt pdf mobi
- 全面解析:中央音乐学院唢呐考级技巧与艺术表现指南
- 大武士瑞奇 pdf epub mobi txt azw3 2024 电子版 下载
- 顽皮小丫的英语征服记·对答如流——顽皮小丫的美国见闻 电子书 下载 txt pdf mobi
- 《灌篮高手》原画集:篮球文化的视觉盛宴与艺术传承
- 成都老鬼 pdf epub mobi txt azw3 2024 电子版 下载
- 华图2025军队文职人员招聘考试专业科目 管理学教材军队文职考试必做题库军队文职人员招聘考试历年真题试卷部队文职管理学考试 电子书 下载 txt pdf mobi
- 探索国际会计的世界:从IFRS基础到公司治理
- 走近SDN/NFV pdf epub mobi txt azw3 2024 电子版 下载
- 报关职业水平测试大纲及试题解析(2017年版) 电子书 下载 txt pdf mobi
- 水泵用无刷直流电动机智能控制系统的MATLAB建模与仿真 龙驹, 曾永忠 西南交通大学出版社【正版】 pdf epub mobi txt azw3 2024 电子版 下载
- 让孩子痴迷的创意折纸书 pdf epub mobi txt azw3 2024 电子版 下载
- 全面掌握Microsoft Access:从基础到高级的数据库管理实战指南
- 钢筋工实训指南:从基础知识到实战应用
- 像美人鱼一样,自由美丽 电子书 下载 txt pdf mobi
- 漫画小小钢琴演奏家—踏板的学问 电子书 下载 txt pdf mobi
- 小人物 pdf epub mobi txt azw3 2024 电子版 下载
- 哈姆莱特 电子书 下载 txt pdf mobi
- 洛克菲勒写给儿子的38封信:财富、成功与人生的智慧